
Advancements in Smart Manufacturing and Industry 4.0: Exploring Technologies and Challenges

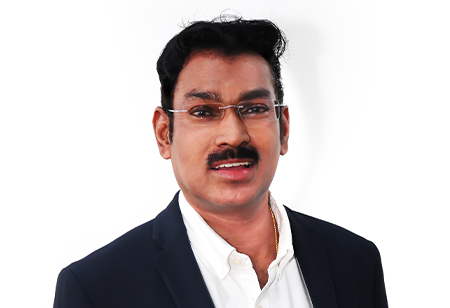
Sekaran Letchumanan, Vice President – Operations, Flex India, 0
In an interaction with CEOInsights India Magazine, Sekaran provides his perspective on the influence of 5G technology within Industry 4.0. He discusses the substantial enhancement in manufacturing processes through integrated automation and robotics, leading to increased efficiency and reduced costs. Further more, he highlights the adoption of cutting-edge technologies by manufacturers to enhance their operational effectiveness and overall profitability.
How do you perceive the impact of 5G on driving Industry 4.0 in India, particularly with enhancing connectivity and enabling real-time data exchange?
5G technology has the potential to revolutionize the manufacturing industry in India. It can enable real-time data processing and analytics, automation, robotics, and remote work. This will lead to improved efficiency, reduced costs, and enhanced safety. 5G will help manufacturers to compete effectively in the global market.
For example, 5G can be used to connect sensors and machines in factories, allowing for real-time data collection and analysis. This data can be used to improve production processes and identify potential problems before they occur. 5G can also be used to power robots and other automated systems in factories, which can lead to increased productivity and reduced costs. Additionally, 5G can be used to enable remote work and training for factory workers, which can help to improve safety and reduce costs.
Overall, the transformative potential of 5G technology is poised to reshape India's manufacturing landscape. It stands to empower manufacturers to thrive on the global stage, creating a dynamic and competitive industry landscape.
What are some of the primary challenges that manufacturers encounter in the supply chain when integrating automation and robotics into their manufacturing processes?
Integrating automation and robotics into manufacturing processes offers advantages such as increased efficiency, reduced costs, and improved safety. However, there are several challenges that must be addressed. The significant initial investment required could be a major hurdle, particularly for smaller manufacturers. Integrating new automation and robotics into existing legacy manufacturing setups might be intricate, necessitating significant retooling and reconfiguration efforts. Additionally, establishing a technology framework that seamlessly integrates hardware and software for continuous monitoring and maintenance of automation and robotics systems can be both time-intensive and costly. The intelligence and real-time decision making is a must-have for customers today because they don’t have that kind of insight on their own.
Are there any specific practices or technologies crucial for safeguarding data integrity and privacy over cloud-based smart manufacturing systems?
To ensure robust data security within cloud-based smart manufacturing, manufacturers must adopt a comprehensive approach. This involves implementing encryption and access control mechanisms to safeguard sensitive data by rendering it unreadable and restricting authorized access. Choosing a trusted cloud service provider is crucial, one that maintains stringent security measures such as firewalls, intrusion detection and prevention systems, and regular security audits. Additionally, consistent system monitoring is vital for promptly identifying and addressing security breaches. Conducting vulnerability scans, penetration tests, and employing security incident and event management systems are indispensable components of a proactive security strategy.
Furthermore, optimizing smart manufacturing through the automation of manufacturing execution system (MES) features can yield significant benefits. This automation enhances production planning, elevates productivity, and mitigates the potential for errors and delays. To fortify the overall security posture, manufacturers should also provide comprehensive training to their workforce. Educating employees about
data security best practices, including the implementation of robust password policies and the limitation of access to sensitive data, is critical.
Which technologies or methods are crucial for accurate predictive maintenance, and how can manufacturers best implement them to enhance production processes?
Industry 4.0 uses predictive maintenance to reduce downtime by analyzing machine data to detect potential problems and schedule maintenance before they happen. This prevents costly breakdowns and associated downtime, and it also helps to streamline maintenance schedules.
Predictive maintenance can help electronics manufacturers to improve operational efficiency and profitability by minimizing downtime, enhancing equipment dependability, reducing maintenance expenses, and optimizing inventory management. This can give manufacturers a competitive advantage by making them more adaptable to market changes.
Advanced technologies including Industrial Internet of Things (IIoT), artificial intelligence (AI), and machine learning allow for the automated collection and analysis of machine data, which makes predictive maintenance possible. This can help to eliminate downtime and improve quality and efficiency, leading to increased revenue, sustainability, and innovation for manufacturers. It can also help manufacturers to be more agile in navigating market fluctuations.
For example, predictive maintenance can be used to prevent costly spindle failures in milling machines. Ultrasonic sensors can be used to collect data on individual spindles, and this data can be analyzed to identify patterns that indicate that a spindle is in danger of failing. This information can then be used to schedule maintenance before the spindle fails, preventing a costly repair.
How should manufacturers use emerging technologies to stay competitive in the changing manufacturing landscape?
As manufacturers look to strengthen their competitive edge in a rapidly evolving landscape, emerging technologies stand out as powerful tools. India's growing market, supported by industry friendly policies, positions the country as an enticing manufacturing hub. Across diverse sectors, the prospects for growth are driving the adoption of advanced manufacturing technologies. These technologies not only address immediate challenges but also lay the foundation for long-term success. Below are some of the key avenues through which manufacturers can embrace innovation and reshape their operations:
•Smart Automation and Robotics: Going beyond pandemic adaptations, automation and robotics offer lasting benefits. They optimize production processes, mitigate downtime, and empower employees to undertake value-added tasks, fostering a more efficient and productive work environment.
•Digitization and Industrial IoT: The Industrial Internet of Things (IIoT) facilitates seamless data sharing, ushering in predictive analytics driven by Artificial Intelligence (AI) and Machine Learning (ML). This predictive capability offers insights into potential equipment failures, enabling proactive maintenance and enhancing operational control.
•Advanced Simulation and Digital Twin: Simulation allows organizations to refine their development processes while conserving resources and time. This agile approach ensures smoother product launches and minimizes potential hiccups. Furthermore, the concept of a Digital Twin emerges as a program that employs real-world data to forecast product and process performance, bestowing advantages like lower operational expenditure (OPEX), heightened automation-driven productivity, and effective error identification.
•Augmented Reality/Virtual Reality: Augmented and virtual reality technologies redefine work procedures by enabling remote collaboration, expediting production line setups, refining training protocols, and creating a foundation for the future dynamics of work.
•Additive Manufacturing: Rapid prototyping through additive manufacturing expedites innovation cycles. This technology enables swift creation of tools, fixtures, and parts, streamlining the design and development phases.
As the manufacturing landscape evolves at a rapid pace, these emerging technologies not only address immediate challenges but also pave the way for long-term success. Embracing these innovations is pivotal for manufacturers looking to navigate this transformative era effectively.
Which technologies or methods are crucial for accurate predictive maintenance, and how can manufacturers best implement them to enhance production processes?
Industry 4.0 uses predictive maintenance to reduce downtime by analyzing machine data to detect potential problems and schedule maintenance before they happen. This prevents costly breakdowns and associated downtime, and it also helps to streamline maintenance schedules.
Predictive maintenance can help electronics manufacturers to improve operational efficiency and profitability by minimizing downtime, enhancing equipment dependability, reducing maintenance expenses, and optimizing inventory management. This can give manufacturers a competitive advantage by making them more adaptable to market changes.
Industry 4.0 uses predictive maintenance to reduce downtime by analyzing machine data to detect potential problems and schedule maintenance before they happen.
Advanced technologies including Industrial Internet of Things (IIoT), artificial intelligence (AI), and machine learning allow for the automated collection and analysis of machine data, which makes predictive maintenance possible. This can help to eliminate downtime and improve quality and efficiency, leading to increased revenue, sustainability, and innovation for manufacturers. It can also help manufacturers to be more agile in navigating market fluctuations.
For example, predictive maintenance can be used to prevent costly spindle failures in milling machines. Ultrasonic sensors can be used to collect data on individual spindles, and this data can be analyzed to identify patterns that indicate that a spindle is in danger of failing. This information can then be used to schedule maintenance before the spindle fails, preventing a costly repair.
How should manufacturers use emerging technologies to stay competitive in the changing manufacturing landscape?
As manufacturers look to strengthen their competitive edge in a rapidly evolving landscape, emerging technologies stand out as powerful tools. India's growing market, supported by industry friendly policies, positions the country as an enticing manufacturing hub. Across diverse sectors, the prospects for growth are driving the adoption of advanced manufacturing technologies. These technologies not only address immediate challenges but also lay the foundation for long-term success. Below are some of the key avenues through which manufacturers can embrace innovation and reshape their operations:
•Smart Automation and Robotics: Going beyond pandemic adaptations, automation and robotics offer lasting benefits. They optimize production processes, mitigate downtime, and empower employees to undertake value-added tasks, fostering a more efficient and productive work environment.
•Digitization and Industrial IoT: The Industrial Internet of Things (IIoT) facilitates seamless data sharing, ushering in predictive analytics driven by Artificial Intelligence (AI) and Machine Learning (ML). This predictive capability offers insights into potential equipment failures, enabling proactive maintenance and enhancing operational control.
•Advanced Simulation and Digital Twin: Simulation allows organizations to refine their development processes while conserving resources and time. This agile approach ensures smoother product launches and minimizes potential hiccups. Furthermore, the concept of a Digital Twin emerges as a program that employs real-world data to forecast product and process performance, bestowing advantages like lower operational expenditure (OPEX), heightened automation-driven productivity, and effective error identification.
•Augmented Reality/Virtual Reality: Augmented and virtual reality technologies redefine work procedures by enabling remote collaboration, expediting production line setups, refining training protocols, and creating a foundation for the future dynamics of work.
•Additive Manufacturing: Rapid prototyping through additive manufacturing expedites innovation cycles. This technology enables swift creation of tools, fixtures, and parts, streamlining the design and development phases.
As the manufacturing landscape evolves at a rapid pace, these emerging technologies not only address immediate challenges but also pave the way for long-term success. Embracing these innovations is pivotal for manufacturers looking to navigate this transformative era effectively.