
Digital Transformation Revolution With Digital Twin Technology

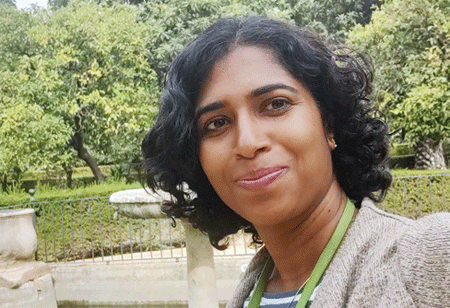
Shirin Hameed, Chief Marketing Officer (CMO), Detroit Engineered Products (DEP), 0
Simulation in as a part of the product development cycle is no longer limited only to the design stage, but extends to design, development, prototyping and manufacturing. And now with digital twins, it extends to the entire life cycle of a product.
What is a Digital twin?
A digital twin is simulated twin of a physical product, it is simply an enabler to convert a physical asset into a numerical asset. They are built to exist along the life of the product, and helps to optimize the real physical asset. A digital twin can be a model of a component, a system of components, or a system of systems - for instance, it can be just the turbine blade of an airplane, or an engine, an entire airplane, or a fleet of airplanes. These digital twins monitor the physical asset, and exchange data and interact through IoT. In the ‘digital twin’, the actual product and the virtual model are no longer separate, but twin-like. It's a digital duplicate that represents a physical object or process, but it is not intended to replace a physical object; it is merely to inform its optimization.
Why is it built?
A common reason for the existence of digital twins is its Operational Optimization. Let us take an example of the oil and gas industry, where currently companies can create an exact replica of their offshore platforms, and connect all the sensors (like accelerometers, vibration/ acoustic measuring devices) at various locations in the platform out in the sea. The digital model or digital twin sits on a computer in an RnD in a computer center on the land. The digital model would also have these similar sensors on them, and the data to them would be piped through the IoT, through the internet.
Through this we can analyse all kinds if information, like how much displacement is caused by certain vibrations, where the stresses are peaking, and are the bolts able to handle these stresses- is there any danger to the platform? This enables system operations to be optimized or controlled during operation to mitigate risk, reduce cost, or gain any number of system efficiencies.
Another a useful function of digital twins is Predictive
maintenance. You can get parameters of how an asset
will perform, in real time to estimate how much of maintenance is really needed. For instance, for an aircraft, you can have a plane in air in flight, and using the digital twin methodology, you will be able to determine whether when it lands, whether maintenance for a part is really needed? If so, where and how much. The maintenance activities can be predicted and planned optimally as a result.
Anomaly detection is another key function of digital twins. You can monitor a system remotely through a system of sensors, and as soon any sensor behaves erratically or goes haywire, it will raise a red flag, and can be checked out before it has a chance to develop into a more serious problem. Essentially, the model runs in parallel to the real assets, and immediately flags operational behaviour that deviates from expected (simulated) behaviour.
The communication channel for digital twins
The information exchange between the digital asset and physical asset happens through iOT. It takes the input from the physical product and passes it on to the digital model( it could CAD, FE or 1D), and generates an output to check if it passes all the parameters.
It is a two way communication channel, where data travels through the physical and numerical worlds back and forth as needed.
What part does CAD/ CAE play in this?
CAE plays a very important role when simulation using digital twin is necessary. CAE builds the numerical model to correlate to actual model, and with the use of digital twins, it has evolved from static input conditions to connected real time input, resulting in better accuracy for development or maintenance of products.
Assume the CAD model is built, the real word data like load conditions, which can be gathered for a machine outside, could be pumped in live to the software, and it can be part of the CAD model. You can also carry it forward to the FE model, and can analyse the FE model with real loads. And thus since your FE model is live, you can communicate directly and have an efficient model suited to real- words conditions.
Changes can be done in the most optimum way in this scenario.
Sometimes FE models could be too heavy, and it could be easier to work with data from Reduced Order Models, like 1 D or 3 D models as well. DEP MeshWorks parametric CAE modeling methodology can be used to create these optimized and parametric FE models, or Response Surface Models, order models, which can be used for analysis.
will perform, in real time to estimate how much of maintenance is really needed. For instance, for an aircraft, you can have a plane in air in flight, and using the digital twin methodology, you will be able to determine whether when it lands, whether maintenance for a part is really needed? If so, where and how much. The maintenance activities can be predicted and planned optimally as a result.
Anomaly detection is another key function of digital twins. You can monitor a system remotely through a system of sensors, and as soon any sensor behaves erratically or goes haywire, it will raise a red flag, and can be checked out before it has a chance to develop into a more serious problem. Essentially, the model runs in parallel to the real assets, and immediately flags operational behaviour that deviates from expected (simulated) behaviour.
The communication channel for digital twins
The information exchange between the digital asset and physical asset happens through iOT. It takes the input from the physical product and passes it on to the digital model( it could CAD, FE or 1D), and generates an output to check if it passes all the parameters.
It is a two way communication channel, where data travels through the physical and numerical worlds back and forth as needed.
A common reason for the existence of digital twins is its operational optimization
What part does CAD/ CAE play in this?
CAE plays a very important role when simulation using digital twin is necessary. CAE builds the numerical model to correlate to actual model, and with the use of digital twins, it has evolved from static input conditions to connected real time input, resulting in better accuracy for development or maintenance of products.
Assume the CAD model is built, the real word data like load conditions, which can be gathered for a machine outside, could be pumped in live to the software, and it can be part of the CAD model. You can also carry it forward to the FE model, and can analyse the FE model with real loads. And thus since your FE model is live, you can communicate directly and have an efficient model suited to real- words conditions.
Changes can be done in the most optimum way in this scenario.
Sometimes FE models could be too heavy, and it could be easier to work with data from Reduced Order Models, like 1 D or 3 D models as well. DEP MeshWorks parametric CAE modeling methodology can be used to create these optimized and parametric FE models, or Response Surface Models, order models, which can be used for analysis.