
Pre Engineered Building : A New Landscape For Indian Construction Sector

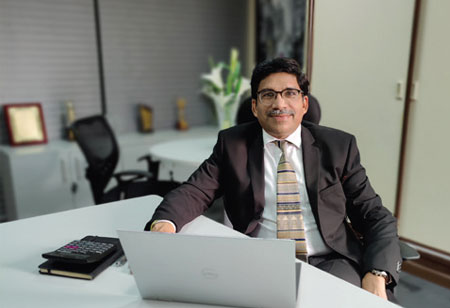
Manish Garg, CEO, Interarch, 0
Civil engineers can witness their physical creations before their eyes, which then stay there for centuries. The profession has come a long way. The mini drafters that we used in our college days are replaced with CAD software; blueprints (called ammonia prints) have also been replaced with white paper prints taken out of giant-sized automatic plotters. The design and analysis carried out by hand calculations have been replaced with computer-aided designs like ETABS, Staad, Robot, and other software. There are terabytes of data stored, all of which can be accessed at the press of a button.
The trends in civil engineering have kept pace with the advancement in technology. The use of project management software like MSP/Primavera, precast concrete members, pre-engineered steel buildings, and offsite construction have contributed to this rapid pace of development.
Pre-Engineered Buildings are one such solution that has revolutionized the Indian construction landscape (particularly for low rise non-residential construction) for over two decades now.
PEBs were unheard of in India until the late midnineties; I first learned about them sometime in 1996 from my mentor and Boss, Gautam Suri. We used to do high-grade Galvalume roofing and wall cladding systems in steel (all imported at that time), with the structural drawings acting as inputs for the design of the roof layout and junction details. All those drawings showed the use of conventional rolled steel sections to form lattice girders/trusses/ lattice columns, bracings, and even purlins and girts were C channels, heavy steel members like trusses. This consumed much steel and took a lot of time to get fabricated 100 percent onsite. It would take us ages before we could begin our roofing work which has to succeed to make this structure work.
‘Necessity is the mother of Invention.’ We needed to find a method to get these steel structures ready quicker so that one could come to the site quickly, install the roofing and cladding, and move to the next job, thereby helping us scale up our business and not be stuck at a place for many months and sometimes years.
We sat down one day, and that’s when we racked our brains to ask, why do we use standard sections? The answer was that standard sections are available and have been used for centuries. Does the section have to be parallel? NO! Then why is it not following the shape of BMD (Bending moment diagram (BMD))?
With my civil engineering background and interest in structural steel design, I quickly found out that if we put steel in the right places and removed the steel from the areas where it is not required, it would be a real game-changer. We picked up one project and tried using plate girders (manually designed) and tried proving to the customer that they were saving at least 30 percent steel in the job and would end up spending much less money. The customer understood our logic and appreciated it but did not agree to use it and went ahead with the conventional approach. However, we were confident that our reasoning was strong and did not lose belief in it.
We went around the world to gather more info, and fortunately, a middle eastern company also came to India during the late 90s and tried doing exactly what we had set out to do. The customers slowly started understanding the logic and felt confident that it was being manufactured in the factory and would save them time and money.
This technology offered significant advantages :
•Saving in construction time
•Factory-made product
•Light and cost-effective buildings
•Peace of Mind, Hassle-free site activities
•And overall great, looking, maintenance-free building
PEBs use high tensile steel to manufacture all components off-site in a factory-controlled environment. The design and engineering are carried out using specialized software like MBS/ Staad and more. The detailing is done using TEKLA and Auto cad. A set of standard products is used repeatedly to create the most efficient designs by iterative methods.
Today more than 50 percent low rise nonresidential buildings are constructed using this technology. Pre-Engineered Buildings have become a default choice for Industrial and warehousing constructions in India.
The industry is valued at more than 10000 Crores and currently growing at a CAGR of more than 10 percent. More than 5-6 tier 1 players 100’s of Tier 2 and 3 players compete for market share. The project management capabilities dictate how good a company is.
Steel is the primary Raw material for these buildings, and a lot depends on how steel market dynamics behave. The steel price fluctuations have been the biggest challenge for the industry in the past two years. GST unavailability as ITC (Input tax credit)for building buildings is another impediment. The government must look into giving this industry infrastructure status and also allow the input credit of GST. There should be regulation of steel prices to the downstream industry. The domestic sector is bound to grow, and the growth can accelerate if a few things mentioned above are also taken care of.
I started working for Interarch as a technical salesman way back in 1994 and would go to structural engineers and architects’ offices to explain the logic we strongly believed in. We would often be very disheartened, but we knew we were breaking conventions, and it always takes time. We had the perseverance to make it work. Today, I can say that with the help of two promoters, we brought the concept of PEB on Indian soil and were fortunate enough to build a BIG business. I enjoyed this journey and created some excellent milestone PEB projects, including Tata Motors Plants and the T3 International Airport terminal.
I then moved on to help set up the PEB Business for another building product giant and was involved there for over 11 years before taking the concept to Africa. I spent another three years with the most prominent building systems company on that continent. Interarch was still growing, and I had to return to India, so I joined Interarch, this time not as a salesman but as their CEO.
I can say PEBs and my belief and conviction in this technology helped me transform from a salesman to a CEO at the same company, Interarch.'
This technology offered significant advantages :
•Saving in construction time
•Factory-made product
•Light and cost-effective buildings
•Peace of Mind, Hassle-free site activities
•And overall great, looking, maintenance-free building
PEBs use high tensile steel to manufacture all components off-site in a factory-controlled environment. The design and engineering are carried out using specialized software like MBS/ Staad and more. The detailing is done using TEKLA and Auto cad. A set of standard products is used repeatedly to create the most efficient designs by iterative methods.
We Needed To Find A Method To Get These Steel Structures Ready Quicker So That One Could Come To The Site Quickly, Install The Roofing And Cladding, And Move To The Next Job, Thereby Helping Us Scale Up Our Business And Not Be Stuck At A Place For Many Months And Sometimes Years
Today more than 50 percent low rise nonresidential buildings are constructed using this technology. Pre-Engineered Buildings have become a default choice for Industrial and warehousing constructions in India.
The industry is valued at more than 10000 Crores and currently growing at a CAGR of more than 10 percent. More than 5-6 tier 1 players 100’s of Tier 2 and 3 players compete for market share. The project management capabilities dictate how good a company is.
Steel is the primary Raw material for these buildings, and a lot depends on how steel market dynamics behave. The steel price fluctuations have been the biggest challenge for the industry in the past two years. GST unavailability as ITC (Input tax credit)for building buildings is another impediment. The government must look into giving this industry infrastructure status and also allow the input credit of GST. There should be regulation of steel prices to the downstream industry. The domestic sector is bound to grow, and the growth can accelerate if a few things mentioned above are also taken care of.
I started working for Interarch as a technical salesman way back in 1994 and would go to structural engineers and architects’ offices to explain the logic we strongly believed in. We would often be very disheartened, but we knew we were breaking conventions, and it always takes time. We had the perseverance to make it work. Today, I can say that with the help of two promoters, we brought the concept of PEB on Indian soil and were fortunate enough to build a BIG business. I enjoyed this journey and created some excellent milestone PEB projects, including Tata Motors Plants and the T3 International Airport terminal.
I then moved on to help set up the PEB Business for another building product giant and was involved there for over 11 years before taking the concept to Africa. I spent another three years with the most prominent building systems company on that continent. Interarch was still growing, and I had to return to India, so I joined Interarch, this time not as a salesman but as their CEO.
I can say PEBs and my belief and conviction in this technology helped me transform from a salesman to a CEO at the same company, Interarch.'