
Quality Management - Today & Tomorrow

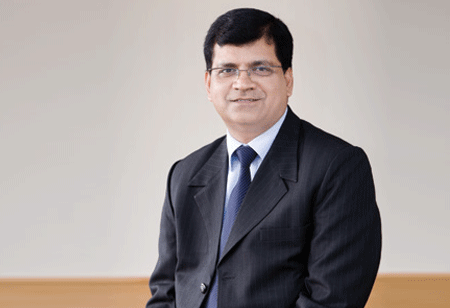
Karuna Pande, Director - Operation, Amazon, 0
Quality management practices have evolved over the years from being a tool for ‘inspectors’ to check and certify products before release to the market to being a partner in designing or making the product/ service. In fact, today the concept of quality management is getting it right at source. Rather than certifying the output it is confirming the inputs because the learning is if the input is right, output has to be. Whether it is related to a product off the shelf/ showroom software developed for a customer or a service provided; the quality of the result is governed by the strict conformance to the design standards by every input that goes into making of the product. Hence, the working is more governed by the systems and standards developed for the purpose instead of it being dependent on the person and his experience or the rigorous checking procedures running into multiple levels.
In recent decades, the idea of quality management has extended beyond the manufacturing floor into the entire value chain from finance to warehousing and every process in between. Quality management in all business processes has become the expectation rather than the exception. Customers increasingly demand suppliers implement effective quality management systems and companies that can’t meet this demand are losing their competitive edge.
Any establishment in which Quality Management is being practiced at all levels will have clear focus on their customer/consumer. We have come across many such examples and to quote one which stands out is the way today’s cab and auto service operates though in very isolated incidents taxi cars or autos have magazines television, WiFi facility and even mobile tablets in their vehicles to delight their customers. The objective is to commute from place A to place B but they are offering their customers more than that and that will make the difference to customer loyalty.
That brings us to the point on what holds the product and service provider towards his customer for the future. With the access to internet on the move, information is available on a click. Consumers/customers are becoming more quality conscious, selective, and prefer affordable high quality products just a call or click away. We hear many stories on how a patient quizzes a doctor
on his ailment quoting alternative treatment methodo-logies. This will call for the doctor to be ahead not only on the medical information but also influencing skills to comfort his patient lest he loses his 'customer'.
A decade from now, the business environment will bear little resemblance to what we see today. The pressure of competition to provide maximum, measurable, predictable and sustainable bottomline results will increase for all levels of management.
Few areas of opportunities that will need attention to today’s business and prepare for the future will be:
•Outsourcing of manufacturing design and transactional processes which have been rampant today will accelerate. Operation excellence through lean management will be the key change driver. We will witness break through products and services mandated by rising customer expectations and made possible by analytics based innovation.
•More attention will be givento green manufacturing, workplace safety, child labor, animal welfare, and product safety. Every activity will be data driven and standardized to reduce variability and improve quality.
•Statistical and visualization tools will be used with maximum effectiveness throughout the value chain. Everyone will have the information needed to perform assigned tasks optimally because software will allow even nontechnical employees to use data.
•The lightning speed at which technology is changing products, services and delivery methods will require organizations to be ever more adaptable and agile. The challenge for quality professional moving into the future will be to undertake Strategic Quality Planning to create a profound impact on the organization’s bottom line.
•Quality Standards will move beyond the realm of work processes into job functions by having them written for all job role functions so that everyone knows not only what is expected of them but exactly what quality standards they must adhere to.
Quality was always important and will continue to be so in the future but the expectations and implications will change many folds. A mass defective product in the market like the current Samsung Note 7 fiasco, will not only lead to product recalls, financial losses and some managers losing jobs but may wipe off the organization itself as the customers will be ever more non for giving.
“Change and innovation are as much attributes of quality and how we manage quality as they are of the products, processes, and services that are produced and delivered.” -A.V. Feigenbaum.
Quality was always important and will continue to be so in the future but the expectations and implications will change many folds
A decade from now, the business environment will bear little resemblance to what we see today. The pressure of competition to provide maximum, measurable, predictable and sustainable bottomline results will increase for all levels of management.
Few areas of opportunities that will need attention to today’s business and prepare for the future will be:
•Outsourcing of manufacturing design and transactional processes which have been rampant today will accelerate. Operation excellence through lean management will be the key change driver. We will witness break through products and services mandated by rising customer expectations and made possible by analytics based innovation.
•More attention will be givento green manufacturing, workplace safety, child labor, animal welfare, and product safety. Every activity will be data driven and standardized to reduce variability and improve quality.
•Statistical and visualization tools will be used with maximum effectiveness throughout the value chain. Everyone will have the information needed to perform assigned tasks optimally because software will allow even nontechnical employees to use data.
•The lightning speed at which technology is changing products, services and delivery methods will require organizations to be ever more adaptable and agile. The challenge for quality professional moving into the future will be to undertake Strategic Quality Planning to create a profound impact on the organization’s bottom line.
•Quality Standards will move beyond the realm of work processes into job functions by having them written for all job role functions so that everyone knows not only what is expected of them but exactly what quality standards they must adhere to.
Quality was always important and will continue to be so in the future but the expectations and implications will change many folds. A mass defective product in the market like the current Samsung Note 7 fiasco, will not only lead to product recalls, financial losses and some managers losing jobs but may wipe off the organization itself as the customers will be ever more non for giving.
“Change and innovation are as much attributes of quality and how we manage quality as they are of the products, processes, and services that are produced and delivered.” -A.V. Feigenbaum.