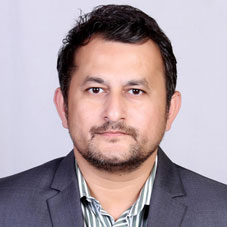
Mahantesh M Jakati
Founder
Today, plastic components are at the heart of innovation, from automotive interiors and electronics housings to lightweight assemblies for EVs. As a result, the pressure is mounting on manufacturers to deliver smarter, faster, and more reliable solutions. Mahantesh M Jakati, Founder of Perfect Technologies stands firmly in this evolving landscape.
He brings a hands-on, practical approach to plastic injection molding and mold manufacturing. Under his leadership, Perfect Technologies has developed end to-end capabilities, from in-house mold design and development to plastic injection molding and high accuracy machining of components.
With an eye on quality and delivery time lines, Mahantesh has led the integration of advanced CNC machinery, 4-axis and 5-axis setups, and cutting-edge design software like ESPRIT and Work NC, making Perfect Technologies a go-to partner for complex, high-tolerance components.
Engaging in an immersive interaction with CEO Insights magazine, Mahantesh shares his leadership approach, future roadmap, and much more. Let's read about it.
What are the key challenges you are currently facing in the industry, and how are you addressing them?
One of the biggest hurdles is the rising cost of raw materials. The constant fluctuations in primary raw materials and auxiliary or consumable materials impact our pricing and production stability.
To manage this, we focus on smarter material utilization, build strong supplier partnerships to negotiate better rates, and adopt lean manufacturing practices to cut down on waste.
Another key challenge is the shortage of skilled manpower. It has become increasingly difficult to find and retain experienced machinists and engineers. We have tackled this by investing in continuous skill development, partnering with technical institutes, and offering clear career paths to encourage retention and growth.
Keeping up with technology is another area we are constantly working on. The pace at which CNC machining and automation is evolving demands consistent upgrades. We have made it a priority to stay ahead by adopting machines such as Citizen, Tsugami, and Mazak, and integrating automation wherever possible to boost productivity and efficiency.
We also face tough competition from global players, especially from low-cost manufacturing regions. Our focus on quality and customer service helps us stand out, and our long-term export relationships with clients in the USA and Italy are proof of that.
Lastly, supply chain disruptions have been a challenge post-pandemic. We have become more resilient by diversifying suppliers, maintaining buffer stocks, and strengthening our planning systems. These challenges keep us agile and push us to innovate continuously.
What best practices do you implement to ensure high levels of customer satisfaction within your team?
We follow strict quality control processes, ensuring every product undergoes thorough inspection using advanced measuring equipment to maintain zero defect standards. Timely delivery is another key focus, and we use efficient production planning, real time monitoring, and smart scheduling tools to meet deadlines without compromising quality.
How are you fostering a culture of innovation, and what new technologies have you adopted in the company?
We constantly upgrade our manufacturing capabilities by investing in cutting-edge machinery. This includes 5-axis CNC machines such as Citizen and Tsugami, as well as 4-axis VMC machines such as Mazak, which allow us to deliver highly complex, tight-tolerance components with unmatched accuracy and speed. Equally important is employee training and development. Our team undergoes regular training on the latest machining techniques, software tools, and quality standards to stay at the forefront of industry trends.
In terms of technological adoption, we have integrated advanced mold-making and plastic injection molding practices using state-of-the-art software such as ESPRIT, WorkNC, and AutoCAD. We have also embraced automation and digital manufacturing to streamline operations, manual
We also face tough competition from global players, especially from low-cost manufacturing regions. Our focus on quality and customer service helps us stand out, and our long-term export relationships with clients in the USA and Italy are proof of that.
Lastly, supply chain disruptions have been a challenge post-pandemic. We have become more resilient by diversifying suppliers, maintaining buffer stocks, and strengthening our planning systems. These challenges keep us agile and push us to innovate continuously.
We blend advanced machinery, smart software, and continuous training to deliver complex, high accuracy components with unmatched speed and efficiency
What best practices do you implement to ensure high levels of customer satisfaction within your team?
We follow strict quality control processes, ensuring every product undergoes thorough inspection using advanced measuring equipment to maintain zero defect standards. Timely delivery is another key focus, and we use efficient production planning, real time monitoring, and smart scheduling tools to meet deadlines without compromising quality.
How are you fostering a culture of innovation, and what new technologies have you adopted in the company?
We constantly upgrade our manufacturing capabilities by investing in cutting-edge machinery. This includes 5-axis CNC machines such as Citizen and Tsugami, as well as 4-axis VMC machines such as Mazak, which allow us to deliver highly complex, tight-tolerance components with unmatched accuracy and speed. Equally important is employee training and development. Our team undergoes regular training on the latest machining techniques, software tools, and quality standards to stay at the forefront of industry trends.
In terms of technological adoption, we have integrated advanced mold-making and plastic injection molding practices using state-of-the-art software such as ESPRIT, WorkNC, and AutoCAD. We have also embraced automation and digital manufacturing to streamline operations, manual
errors, and boost efficiency.
How would you describe your leadership style and the core methodologies you follow?
I focus on driving long-term strategic growth while ensuring operational excellence through investments in advanced technology and continuous improvement. I strongly believe in empowering my team by encouraging open communi- cation, skill develop-ment, and a sense of ownership at every level. My methodology includes lean manufacturing, process optimization, employee development programs, data driven decisions, and collaborative leadership.
What is your outlook on the future of the market?
I see strong growth opportunities in the manufacturing and plastic injection molding industry. The demand for components is steadily rising across various sectors such as automotive, electronics, medical devices, industrial automation, and electrical equipment. One of the key market trends is the increasing demand for high-tolerance CNC-machined components as industries continue to push for higher efficiency, miniaturization, and superior product quality.
The expansion of the electric vehicle (EV) sector is another major driver. With the global shift toward EVs and sustainable mobility, there's a growing requirement for lightweight, engineered parts, and molded components for batteries, sensors, and other critical assemblies. Further, the rise of automation and smart manufacturing is creating demand for customized components that support robotics and digital production systems. At Perfect Technologies, we are well-positioned to capitalize on these opportunities by strengthening customer relation- ships, investing in innovation, and continuing to deliver solutions that meet global standards.
Mahantesh M Jakati, Founder, Perfect Techno- logies
Mahantesh M Jakati, Founder of Perfect Technologies is a passionate entrepreneur and industry professional with deep expertise in plastic injection molding, precision mold making, and high-accuracy machining. He has been instrumental in driving technology-led growth and delivering high-quality engineering solutions across sectors like automotive and electronics.
•Hobbies: Reading, Playing Chess
•Favorite Cuisine: Indian
•Favorite Book: The Bhagavad Gita
•Awards and Recognition: Best Supplier Award from Minda Industries and Best Supplier Award from German Hitachi Automotive.
How would you describe your leadership style and the core methodologies you follow?
I focus on driving long-term strategic growth while ensuring operational excellence through investments in advanced technology and continuous improvement. I strongly believe in empowering my team by encouraging open communi- cation, skill develop-ment, and a sense of ownership at every level. My methodology includes lean manufacturing, process optimization, employee development programs, data driven decisions, and collaborative leadership.
What is your outlook on the future of the market?
I see strong growth opportunities in the manufacturing and plastic injection molding industry. The demand for components is steadily rising across various sectors such as automotive, electronics, medical devices, industrial automation, and electrical equipment. One of the key market trends is the increasing demand for high-tolerance CNC-machined components as industries continue to push for higher efficiency, miniaturization, and superior product quality.
The expansion of the electric vehicle (EV) sector is another major driver. With the global shift toward EVs and sustainable mobility, there's a growing requirement for lightweight, engineered parts, and molded components for batteries, sensors, and other critical assemblies. Further, the rise of automation and smart manufacturing is creating demand for customized components that support robotics and digital production systems. At Perfect Technologies, we are well-positioned to capitalize on these opportunities by strengthening customer relation- ships, investing in innovation, and continuing to deliver solutions that meet global standards.
Mahantesh M Jakati, Founder, Perfect Techno- logies
Mahantesh M Jakati, Founder of Perfect Technologies is a passionate entrepreneur and industry professional with deep expertise in plastic injection molding, precision mold making, and high-accuracy machining. He has been instrumental in driving technology-led growth and delivering high-quality engineering solutions across sectors like automotive and electronics.
•Hobbies: Reading, Playing Chess
•Favorite Cuisine: Indian
•Favorite Book: The Bhagavad Gita
•Awards and Recognition: Best Supplier Award from Minda Industries and Best Supplier Award from German Hitachi Automotive.